OPERATIONS » HEALTH AND SAFETY
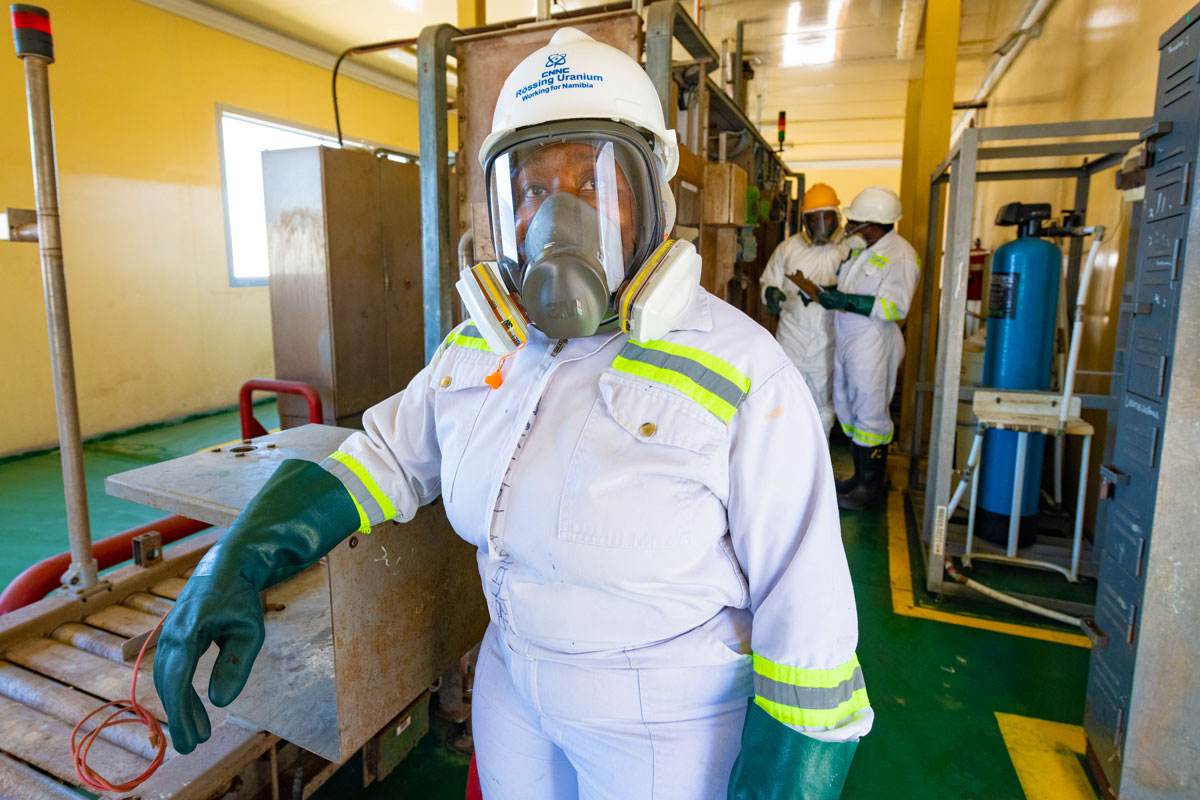
Occupational Health Management
Our occupational health programmes focus on early detection, prevention, and management of work-related health risks.
Regular health screenings, workplace exposure monitoring, and wellness initiatives ensure a proactive approach to employee well-being.
We also comply with all Namibian legal and regulatory health requirements, aligning with best practices in workplace health management.
Safety Metrics and Initiatives
We track and analyse key safety performance indicators to measure our effectiveness and identify areas for improvement.
Our Life Saving Rules (LSRs) and Critical Risk Management (CRM) frameworks focus on eliminating potential fatal incidents (PFIs) by ensuring that critical controls are consistently implemented and verified across all operations.
Life Saving Rules (LSRs)
Our Life Saving Rules provide clear guidelines on critical behaviours and controls necessary to prevent life-threatening incidents. These rules serve as the foundation of our safety culture and are reinforced through regular training, visual reminders, and audits across operational sites.
Critical Risk Management (CRM)
CRM is designed to prevent fatal and permanently disabling injuries by focusing on the selection, verification, and evaluation of critical controls. This approach ensures high-risk activities undergo thorough planning, verification, and execution to prevent safety breaches.
Key safety initiatives include:
- Process Safety Management – Preventing hazardous incidents through stringent risk assessments and control measures.
- Incident Reporting and Investigation – Learning from incidents to strengthen preventive measures.
- Emergency Preparedness – Regular drills and response training to handle potential workplace hazards effectively.
By embedding these principles, Rössing Uranium remains committed to a proactive safety culture, continuous improvement, and risk reduction at all operational levels.
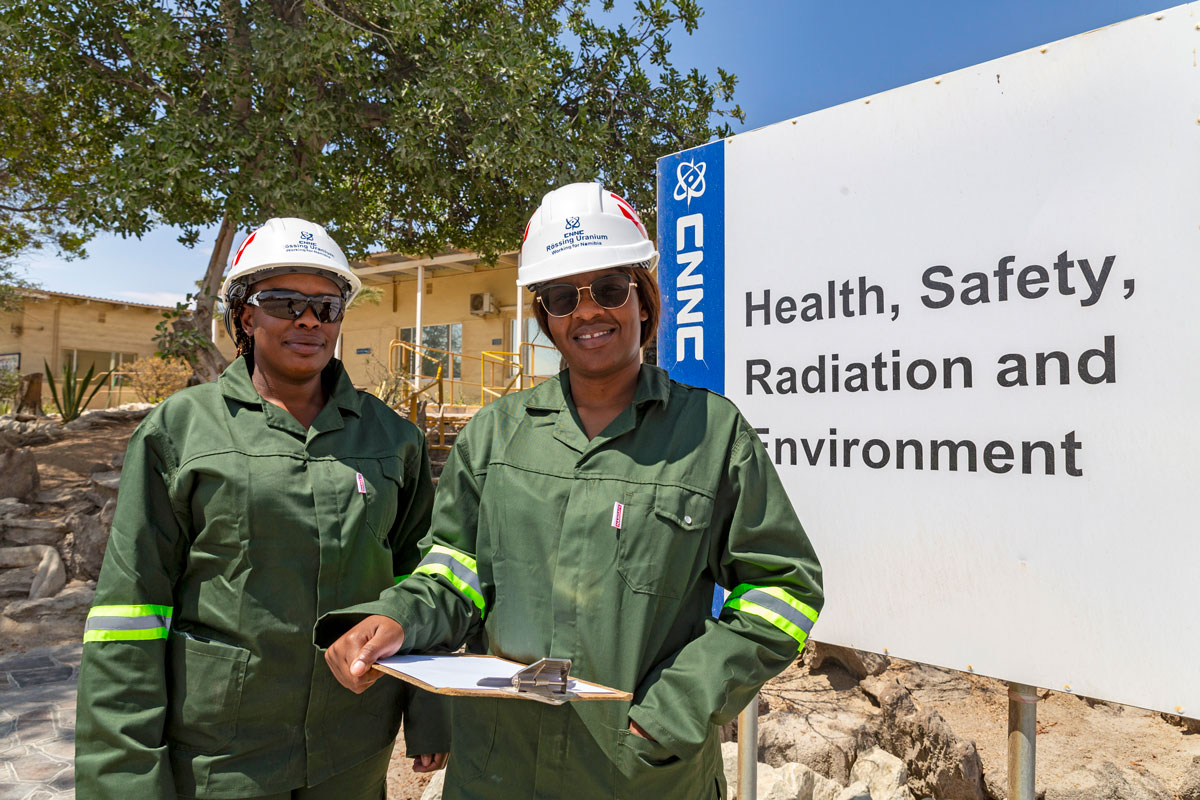
HSE Management
Rössing Uranium operates under a structured 15-point Health, Safety, Environment & Protection Services (HSE & PS) Management System, which is periodically audited and updated to align with industry standards.
This system ensures compliance with legal and regulatory requirements, integrates hazard and risk management, and continuously improves workplace safety and environmental sustainability.
By embedding these principles into our daily operations, Rössing Uranium remains committed to a culture of safety, continuous improvement, and proactive risk management.